Cavalleri CT12 sheeter (Revamping 2024)
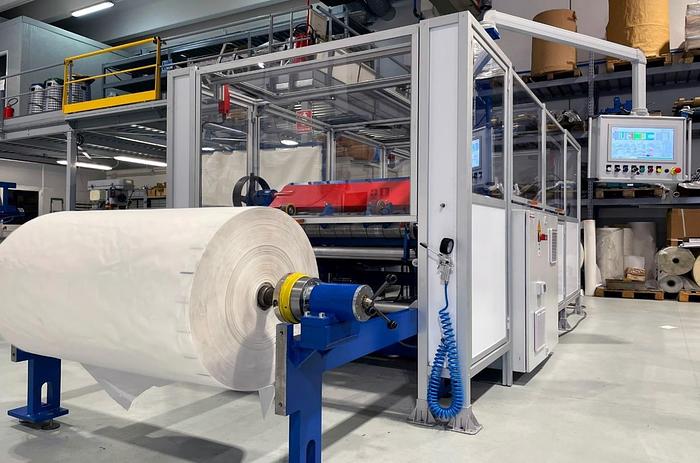
Cavalleri CT12 sheeter (Revamping 2024)
Lokalizacja:Włochy
Opis
We submit to your attention a CAVALLERI sheeter model CT12 REVAMPING.
The machine allows to process paper (such as tissue paper, parchment paper, countertop paper, wrapping paper), cardboard, laminated materials (paper and cartene, polythene paper), self-adhesive paper, silicon paper and others in weights from 18 to 250 g/m², aluminum and plastic materials (such as polypropylene, polyethylene) within thicknesses from 30 to 200 μm.
The machine is of years 1990s but is sold with a complete revamping performed in 2024 (with 12 months warranty) of both the mechanical and electronic parts of the machine.
The machine have new with Schneider Electric automation, with the possibility of being networked for remote assistance.
The following are the primary new features of the sheeter as a result of the revamping operation:
- allows to set the amount of sheets held by the grippers of the collecting cylinder (between 5 and 30 sheets) and the trolley bar directly from the control panel, even when the machine is running.
- allows the speed at which the sheets are released onto the collection table to be set from the control panel;
- avoids the need for the operator to make mechanical adjustment, using a 22 mm wrench, of the collection cylinder at each change of cutting format;
- avoids mechanical maintenance of the gear box
Specyfikacje
Producent | Cavalleri |
Model | CT12 |
Stan | Odnowione |
Max. reel width | 1000 mm |
Max. blade span | 1050 mm |
Max. reel diameter | 1050 mm |
Max. reel weight | 1000 Kg |
Reel core diameter | 76 mm |
Min. format length | 250 mm |
Max. format length | 1010 mm |
Max speed | 120 cuts/min (depending on the material and format) |
Cutting accuracy | ± 0,5 mm (depending on the material and printing) |
Material | Paper (such as tissue paper, parchment paper, countertop paper, wrapping paper), cardboard, laminated materials (paper and cartene, polythene paper), self-adhesive paper, silicon paper and others in weights from 18 to 250 g/m², aluminum and plastic materials (such as polypropylene, polyethylene) within thicknesses from 30 to 200 μm. |
Register control | No. 1 optical unit for cutting a centered print reel |
4 motors upgrade | Oil-bath gearbox removal and installation of 2 additional electric axis motors for collecting drum and trolley bar, respectively. Below are the main new features resulting from the upgrade: - allows you to set the amount of sheets held by the clamps on the collecting drum directly from the control panel, even while the machine is running; - allows you to collect between 5 and 30 sheets on the collecting drum; - allows the speed at which the sheets are released onto the collection table to be set from the control panel; - avoids the operator's task of mechanically adjusting the collection drum at each change of cutting format - avoids mechanical maintenance of the gear box |
Pneumatic unwinder | With integrated electronic control board |
Static charges removal system | Simple efficiency antistatic unit consisting of a feeder and three bars |
Air generation system | Studied for for material weighing less than 50 g/m² |
Safety stop devices | They automatically trigger by pressing the emergency stop buttons. The micro-switches of the covers have interlocked double protection, in order to prevent the opening of the safety guards while the machine is running. In addition, a manual operation procedure is provided that allows the operator to do adjustments with opened carters in complete safety. |
Aluminium and lexan anti-accident security guards | Protection systems according to the standards of the regulations in force |
Work performed / revamping | Total disassembly of the sheeter with replacement or overhaul of the following parts: - Frame disassembly and painting in RAL 5010 blue color - Disassembly of moving parts and painting - Replacement of all bearings with new ones of SKF/FAG brand - Replacement of 3 collector cylinder cams with new ones made of hardened steel - Replacement of 5-sheet cam with new one of hardened steel - Replacement of chains and crowns of the trolley bar - Replacement of chains of the high stack table - Replacement of all clamps of both the trolley bar and the collecting drum - Replacement of all conveyor belts - Replacing damaged timing belts and checking the others - Replacement of all cutting blades - Total overhaul of the collecting drum and of the trolley bar - Removal of oil-bath gearbox - Installation of new electric system, touch screen panel, digital drives and 4 brushless motors - Installation of new software - Installation of safety electrical system - Installation of guards and protections to CE standards - Mechanical, electrical, visual functional test |
Max electric power | 10 kW |
Noise emission | < 76 dB(A) |
Documentation and Certifications | CE Conformity Declaration | User and maintenance instruction manuals in English | Electric drawings. |
Visible in operation | Yes | possibility to test the sheeter also with the material of the customer |